Tailor made exhaust gas system
As Ecoexhaust, we offer the complete customized exhaust gas systems, mainly but not limited, to the Marine & Offshore market. Our, highly skilled and experience team, based on the; gained knowledge through the dozen years working at Marine & Offshore industry, unique approach to engineering and use of modern software aid, is capable to design and delivery of exhaust gas systems solutions which fulfils any stated requirements by Client/Class/Environmental for following applications:
-
Marine industry â all kind of watercrafts
-
Offshore â oil/gas platforms or accommodation platforms
-
Onshore â generators for plants, Labs, data centers, emergency systems, cogenerations etc.
In general the exhaust gas systems are categorized into main two types:
-
Wet system – characterized by sea water injection system to cool down flue gas down to temp. of 60 C°. The part of the system, where sea water injection starts is to be made of titanium (optionally high grade stainless steel, such us: SMO, Duplex or AISI 904l). For watercrafts applications the wet exhaust gas discharge outlet for to be mainly located close to the water line, for instance: within water line, above water, underwater with bypass above water line or at the aft/transom of the vessel.
-
Dry system – standard âchimneyâ systems where components are made of stainless steel or carbon steel through-out the complete system
In order to provide reliable as well as cost effective products to our Customers, Ecoexhaust performs comprehensive analysis to optimize design as well as validate engineering approach, where the following simulations are being performed :
-
CFD analysis
-
Acoustic analysis
-
Structural analysis
During years, performing several dozen projects mostly in marine industry, we gained extensive experience working with various Classification Societies such us: DNV GL, Bureau Veritas, Lloydâs, CCS, PRS, RINA etc. Thus, in case project requires, our systems will be designed and produced to comply with relevant Class requirements and our company will follow up the complete certification process.
In the below diagram we present typical wet exhaust gas system with SCR system (for instance IMO Tier 3 compliant) or DPF system in case of emission requirements shall be followed for Navy or Super Yachts application. Combination of two silencers: absorption and reflection allows to achieve noise level of 75-80 dB(A), or even lower. Special wire isolator are applied to comply with relevant vibration/shock requirements, for instance: COMF-V etc. ATEX/IECEx housings for electrical equipment can be used in case systems shall operate in hazardous areas or be installed at Navy vessels.
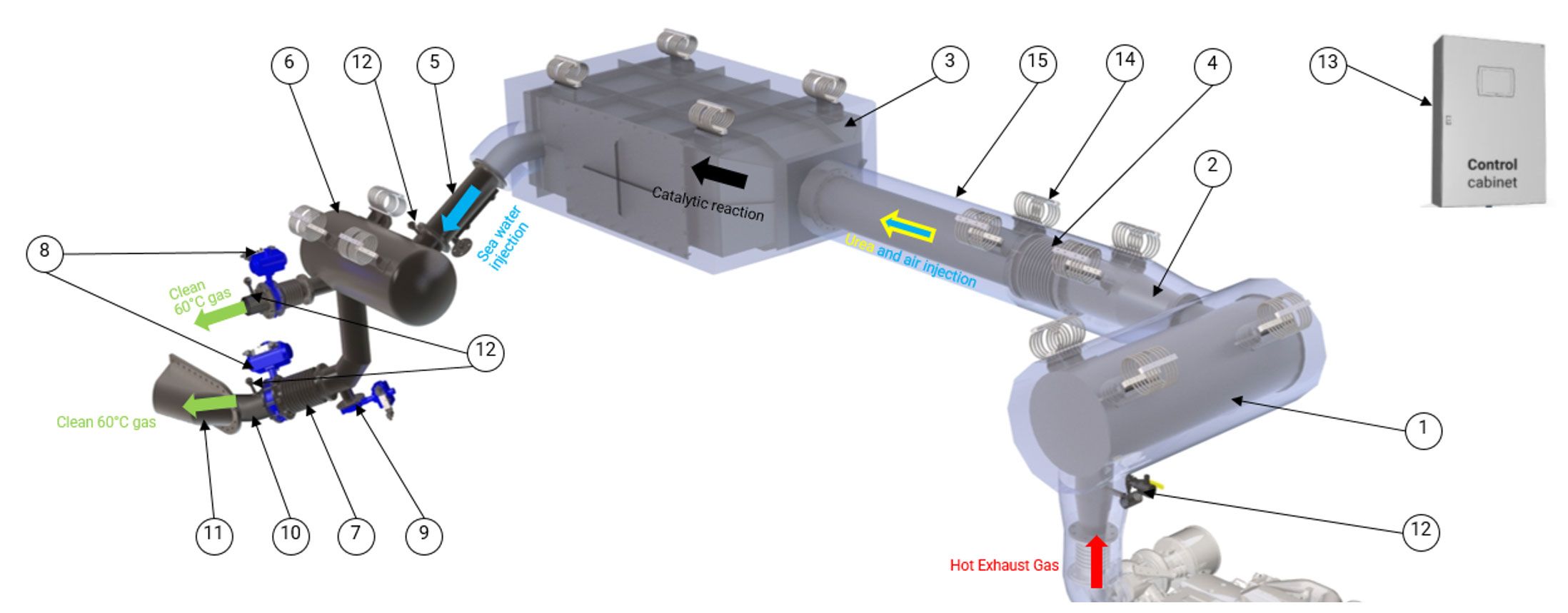
ID# | Item name | Description |
1 | Dry Silencer | Made of stainless steel, designed as an absorption type silencers with attenuation level adjusted to project requirements. Combination of Dry absorption silencer, SCR reactor as well as reflection Wet silencers, allows to achieve noise level of 75 (dBA) simultaneously keeping the back pressure within max. permissible level |
2 | Dry Exhaust piping before sea water injection | Made of stainless steel, design to handle exhaust gas keeping its velocity between 40-50 m/s and with min. thickness to reduce weight of the complete system |
3 | SCR system (SCR Reactor and Mixing Tube) or DPF filter | SCR reactor, urea mixing tube, Or Particulate matter reduction DPF filter are typically made of chrome moly steel or stainless steel. For more details, please see solutions |
4 | Dry Compensator/s before sea water injection | Made of stainless steel, compensating all movements in the systems caused by thermal expansion, vibration, pressure picks or shock |
5 | Sea water injector and sea water supply system | Made of titanium, For more details, please see solutions |
6 | Wet silencer | Made of titanium, deigned as reflection type silencer with approx. noise attenuation level of 10-18 dBA. Contains additional secondary sea water injection at outlet side. |
7 | Wet Compensator/s after sea water injection | Inner layer of the compensator in a wet part is manufactured in titanium for the purpose of corrosion resistance, whereas the outer layer is made of stainless steel., compensating all movements in the systems caused by thermal expansion, vibration. pressure picks or shock |
8 | Hull Valve and by-pass hull valve | Butterfly Wafer type valve, depends on requirements and exhaust gas discharge outlet solution, either: – equipped with manual lever – or pneumatic double acting actuator and solenoid valve for automatic open/close operation based on inputs from engine PLC. |
9 | Drain valve | Butterfly Wafer type valve, allows draining of remaining sea water from the system while engine operation is stopped and hull valve is being closed. |
10 | Hull penetration | Made of same material as vesselâs hull, normally shipyard scope of supply manufactured and weld on place acc. to EcoExhaustâs drawings and recommendations. |
11 | Protection Cap/Scoop | Made of the same material as hull as well as with the same coating systems, weld/bolted on place acc. to EcoExhaust drawings and recommendations. Item can be also made of high grade stainless steels. |
12 | Instrumentation | Systems are equipped with relevant instrumentation to monitor: Exhaust gas back pressure, Sea water injection pressure , Temperature of exhaust gas, SCR NOx reduction, SCR differential pressure at inlet and outlet of SCR reactor and Temperature of exhaust gas at the outlet of SCR reactor. Sensors can be provided as standard in plastic body or in case project requires in ATEX/IECEx approved housing. |
13 | PLC for exhaust gas system and SCR system | Tailor-made PLC system fitted into the Cabinet (if required, in ATEX/IECEx approved cabinets) controlling and monitoring exhaust gas systems units as well as SCR system, including user friendly HMI or integrated into engineâs PLC with main functions such us: – Monitoring of: as given at point 12 for Instrumentation – Control and monitoring Urea and Air dosing system – Controlling opening and closing of Hull Valve and Drain valve – Controlling of sea water flow, in case relevant sea water flow regulating valve is needed in the system – Controlling the sea water pump operation, in case separate electrically driven sea water pump is needed for exhaust cooling process – Alarms and emergency operation handling |
14 | Flexible supports | Depends on requirements either standard exhaust gas systems suspensions are applied or wire isolator where relevant vibration or sock requirements shall be followed. |
15 | Thermal insulation | Based on project spec. the relevant thermal insulation can be provided either as mineral wool with stainless steel jacketing or insulation mats which allows friendly service and maintenance as well as weight reduction of complete systems. |
ID# | Description |
1 | Dry Silencer Made of stainless steel, designed as an absorption type silencers with attenuation level adjusted to project requirements. Combination of Dry absorption silencer, SCR reactor as well as reflection Wet silencers, allows to achieve noise level of 75 (dBA) simultaneously keeping the back pressure within max. permissible level |
2 | Dry Exhaust piping before sea water injection Made of stainless steel, design to handle exhaust gas keeping its velocity between 40-50 m/s and with min. thickness to reduce weight of the complete system |
3 | SCR system (SCR Reactor and Mixing Tube) or DPF filter SCR reactor, urea mixing tube, Or Particulate matter reduction DPF filter are typically made of chrome moly steel or stainless steel. For more details, please see solutions |
4 | Dry Compensator/s before sea water injection Made of stainless steel, compensating all movements in the systems caused by thermal expansion, vibration, pressure picks or shock |
5 | Sea water injector and sea water supply system Made of titanium, For more details, please see solutions |
6 | Wet silencer Made of titanium, deigned as reflection type silencer with approx. noise attenuation level of 10-18 dBA. Contains additional secondary sea water injection at outlet side. |
7 | Wet Compensator/s after sea water injection Inner layer of the compensator in a wet part is manufactured in titanium for the purpose of corrosion resistance, whereas the outer layer is made of stainless steel., compensating all movements in the systems caused by thermal expansion, vibration. pressure picks or shock |
8 | Hull Valve and by-pass hull valve Butterfly Wafer type valve, depends on requirements and exhaust gas discharge outlet solution, either: – equipped with manual lever – or pneumatic double acting actuator and solenoid valve for automatic open/close operation based on inputs from engine PLC. |
9 | Drain valve Butterfly Wafer type valve, allows draining of remaining sea water from the system while engine operation is stopped and hull valve is being closed. |
10 | Hull penetration Made of same material as vesselâs hull, normally shipyard scope of supply manufactured and weld on place acc. to EcoExhaustâs drawings and recommendations. |
11 | Protection Cap/Scoop Made of the same material as hull as well as with the same coating systems, weld/bolted on place acc. to EcoExhaust drawings and recommendations. Item can be also made of high grade stainless steels. |
12 | Instrumentation Systems are equipped with relevant instrumentation to monitor: Exhaust gas back pressure, Sea water injection pressure , Temperature of exhaust gas, SCR NOx reduction, SCR differential pressure at inlet and outlet of SCR reactor and Temperature of exhaust gas at the outlet of SCR reactor. Sensors can be provided as standard in plastic body or in case project requires in ATEX/IECEx approved housing. |
13 | PLC for exhaust gas system and SCR system Tailor-made PLC system fitted into the Cabinet (if required, in ATEX/IECEx approved cabinets) controlling and monitoring exhaust gas systems units as well as SCR system, including user friendly HMI or integrated into engineâs PLC with main functions such us: – Monitoring of: as given at point 12 for Instrumentation – Control and monitoring Urea and Air dosing system – Controlling opening and closing of Hull Valve and Drain valve – Controlling of sea water flow, in case relevant sea water flow regulating valve is needed in the system – Controlling the sea water pump operation, in case separate electrically driven sea water pump is needed for exhaust cooling process – Alarms and emergency operation handling |
14 | Flexible supports Depends on requirements either standard exhaust gas systems suspensions are applied or wire isolator where relevant vibration or sock requirements shall be followed. |
15 | Thermal insulation Based on project spec. the relevant thermal insulation can be provided either as mineral wool with stainless steel jacketing or insulation mats which allows friendly service and maintenance as well as weight reduction of complete systems. |
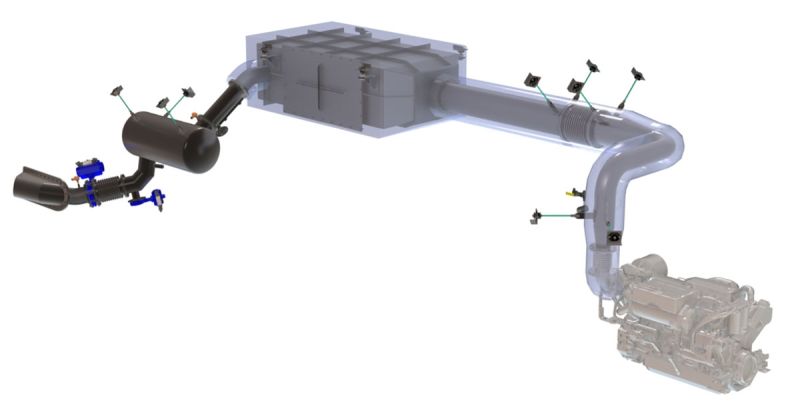
Typical wet exhaust gas system with SCR system (for instance IMO Tier 3 compliant) or DPF system without specific noise and vibration/shock requirements for application at high speed catamarans, ferries, yachts/superyachts.
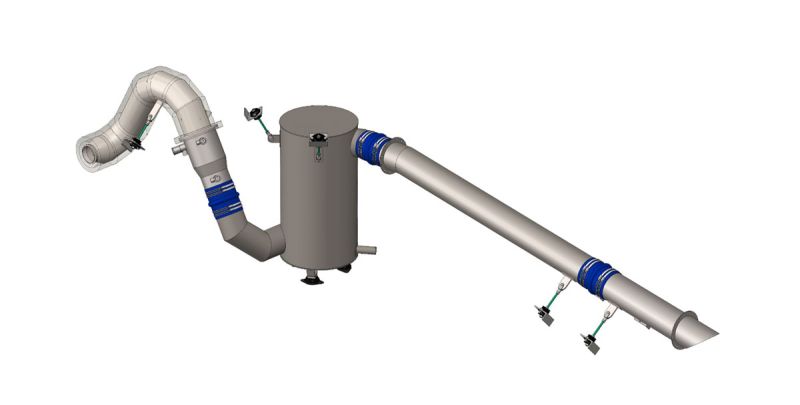
Typical wet exhaust gas system with sea water spray ring and lift muffler for application at smaller pleasure boats / yachts.
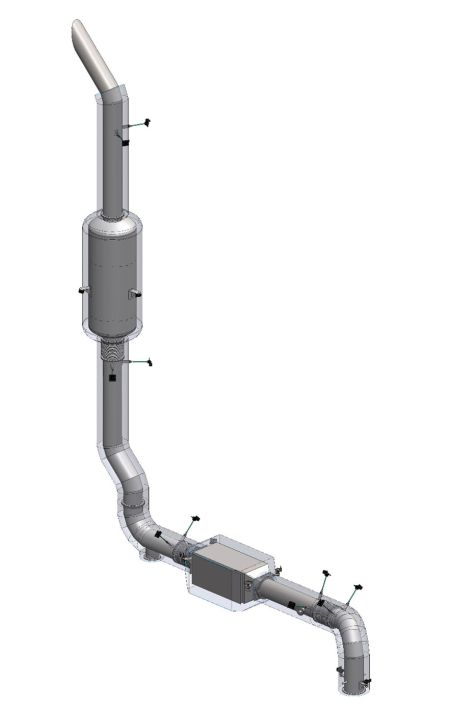
Typical dry exhaust gas system with exhaust gas aftertreatment (SCR/DPF) for applications such us: cargo vessels, supply vessels or onshore installations
Contact us
Our team is happy to answer any questions.
Contact
-
Bruzdowa 106a/13
02-991 Warsaw
woj. mazowieckie
Poland -
+48 506 508 330
+48 600 501 050 -
info@ecoexhaust.eu